





摘要 溫度過低不僅達不到除垢除銹的目的,而且影響鈍化效果,無法形成致密的鈍化膜,造成重大經(jīng)濟損失。
1 前言
鍋爐化學清洗包括新爐的煮爐和舊爐的除垢,煮爐過程為:水沖洗、堿洗脫脂、堿洗后水沖洗、酸洗、酸洗后的水沖洗、漂洗、中和鈍化。清洗過程中溫度控制極為重要,溫度過高不利于現(xiàn)場控制,還會造成鍋爐新的腐蝕,而溫度過低則達不到酸洗除垢的目的,同時溫度過低還會影響鈍化效果,無法形成致密的保護膜。齊魯石化公司熱電廠5#爐就發(fā)生了清洗時溫度過低而清洗質(zhì)量的事故。
2 概述
熱電廠5#爐HG410/100-11型自然循環(huán)單汽包單段蒸發(fā)集中下降管、尾部雙級布置的鍋爐。鍋爐四周布滿水冷壁,爐膛出口處布置屏式過熱器,水平煙道處為兩級對流過熱器,尾部豎井交錯,布置2級省煤器和2級空氣預熱器,爐頂水平煙道轉(zhuǎn)向室和尾部包墻均用鰭片包敷。汽包直徑1600mm,筒身厚90mm,筒身長1300mm,封頭壁厚100mm,汽包全長14520mm,汽包內(nèi)設有56個(315旋風分離器,汽包內(nèi)還設有磷酸鹽加藥裝置和連排裝置,鍋爐爐堂四周布滿60×5節(jié)距為80mm的鰭片管焊全密封的膜式水冷壁,爐膛四壁共4×124根上升管,7根(377×25集中下降管從汽包最低點引出至運轉(zhuǎn)層以下,再以48根(133×10的連接管分散引入水冷壁下集箱,前水冷壁、后水冷壁、和側(cè)水冷壁上集箱公用42根(133×10的汽水引出管,斜包墻上集箱用12根(133×10汽水引出管同汽包相連接。
本次化學清洗是本臺鍋爐第一次清洗,由施工單位負責。其主要目的是脫脂除銹、清洗焊渣、鈍化,保證鍋爐初次運行的安全和水汽品質(zhì)。清洗范圍為省煤器、水冷壁、下降管、汽包。
3 化學清洗工藝控制
3.1 化學清洗工藝設計
3.1.1 堿洗:用0.05%洗滌劑+0.05%Na3PO4+0.2%Na2HPO4溶液循環(huán)清洗12h,清洗溫度為80-90℃。
3.1.2 堿洗后水沖洗:用除鹽水沖洗至出水PH=8.4,水質(zhì)透明,放盡沖洗水,檢查系統(tǒng)中有否焊接口泄漏或其它缺陷,如有應立即消除。以減少化學清洗時可能出現(xiàn)的問題,并準備足夠的除鹽水。
3.1.3 酸洗:在5%HCI+0.3%TP-1緩蝕劑+0.5%酸脲+0.5%NaF溶液中循環(huán)清洗8~10h,酸洗液溫度為50(5℃,酸洗滌過程應加強酸液濃度和鐵離子濃度的分析。檢查是否達到了平衡并取下監(jiān)視管檢查酸洗效果。當酸洗過程中鐵離子濃度趨穩(wěn)定,監(jiān)視管內(nèi)基本清洗,再循環(huán)1h左右便可停止酸洗。
3.1.4酸洗后水沖洗:酸洗后如有較多的未溶解沉渣堆集在清洗系統(tǒng)的死角時,可在酸洗液排盡后,用水沖洗至出水pH=4~5時排放,用人工清理汽包、集箱和下集箱手孔內(nèi)的沉渣。
3.1.5 鈍化:鈍化液維持N2H4濃度為200~300mg/L,pH=9.5~10,在90(5℃的鈍化液中循環(huán)24h后熱爐放水,與此同時,在廢液處理池中放入NaCl溶液進行分解,處理到N2H2<10ug/L。
3.2.1 I回路:
3.3 化學清洗過程的監(jiān)督
由于現(xiàn)場施工時對拌熱管線管徑未經(jīng)計算,管徑過細且鍋爐入口管線未加保溫層,實際清洗過程溫度偏低,堿洗時溫度最高只有43℃,酸洗時清洗箱液體溫度滿足不了酸洗的工藝要求,只有35℃左右,因此整個酸洗過程基本是在室溫下進行的。整個酸洗過程由下午13:00開始,23:00結(jié)束。分析結(jié)果見酸洗過程監(jiān)測表3~1:
表3-1 酸洗過程監(jiān)測表
時間 |
酸度( % ) |
鐵離子( mg/L ) |
||
入口 |
出口 |
Fe2+ |
Fe3+ |
|
14 : 20 |
2.7 |
1.2 |
||
15 : 05 |
3.9 |
3.5 |
5.5 |
56 |
15 : 30 |
4.2 |
2.6 |
||
16 : 15 |
4.7 |
3.7 |
||
17 : 15 |
3.8 |
3.4 |
||
17 : 30 |
3.6 |
2.8 |
|
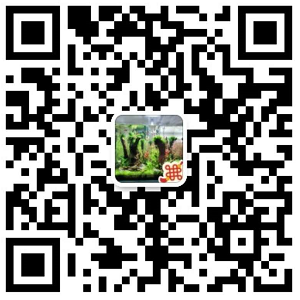